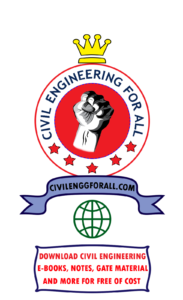
CONTENTS OF THE BOOK
1. Structural Analysis – Stiffness Method
- Introduction
- Degrees of Freedom and Indeterminacy
- Statically Indeterminate Structures—Direct Stiffness Method
- Member Stiffness Matrix
- Coordinates Transformation
- Member Stiffness Matrix in Global Coordinate System
- Assembly of Structure Stiffness Matrix
- Load Vector
- Methods of Solution
- Calculation of Member Forces
- Treatment of Internal Loads
- Treatment of Pins
- Temperature Effects
2. Plastic Behaviour of Structures
- Introduction
- Elastic and Plastic Behaviour of Steel
- Moment–Curvature Relationship in an Elastic–Plastic Range
- Plastic Hinge
- Plastic Design Concept
- Comparison of Linear Elastic and Plastic Designs
- Limit States Design
- Overview of Design Codes for Plastic Design
- Limitations of Plastic Design Method
- Plastic Flow Rule and Elastoplastic Analysis
- General Elastoplastic Analysis of Structures
- Reduced Plastic Moment Capacity Due to Force Interaction
- Concept of Yield Surface
- Yield Surface and Plastic Flow Rule
- Derivation of General Elastoplastic Stiffness Matrices
- Elastoplastic Stiffness Matrices for Sections
- Stiffness Matrix and Elastoplastic Analysis
- Modified End Actions
- Linearized Yield Surface
4. Incremental Elastoplastic Analysis—Hinge by Hinge Method
- Introduction
- Use of Computers for Elastoplastic Analysis
- Use of Spreadsheet for Automated Analysis
- Calculation of Design Actions and Deflections
- Effect of Force Interaction on Plastic Collapse
- Plastic Hinge Unloading
- Distributed Loads in Elastoplastic Analysis
5. Manual Methods of Plastic Analysis
- Introduction
- Theorems of Plasticity
- Mechanism Method
- Statical Method
- Uniformly Distributed Loads (UDL)
- Continuous Beams and Frames
- Calculation of Member Forces at Collapse
- Effect of Axial Force on Plastic Collapse Load
6. Limit Analysis by Linear Programming
- Introduction
- Limit Analysis Theorems as Constrained Optimization
- Spreadsheet Solution of Simple Limit Analysis
- General Description of the Discrete Plane Frame
- A Simple MATLAB Implementation for Static Limit Analysis
- A Note on Optimal Plastic Design of Frames
7. Factors Affecting Plastic Collapse
- Introduction
- Plastic Rotation Capacity
- Effect of Settlement
- Effect of High Temperature
- Second-Order Effects
8. Design Consideration
- Introduction
- Serviceability Limit State Requirements
- Ultimate Limit State Requirements
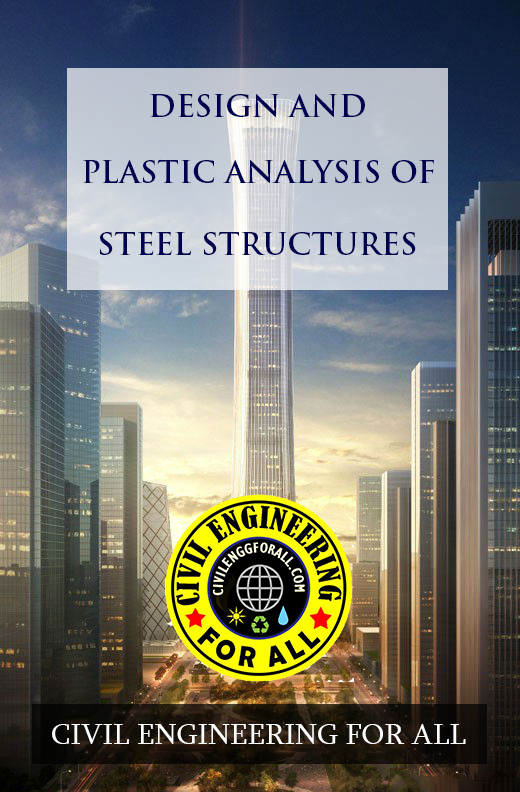
Degrees of Freedom and Indeterminacy
Plastic analysis is used to obtain the behaviour of a structure at collapse. As the structure approaches its collapse state when the loads are increasing, the structure becomes increasingly flexible in its stiffness. Its flexibility at any stage of loading is related to the degree of statical indeterminacy, which keeps decreasing as plastic hinges occur with the increasing loads. This section aims to describe a method to distinguish between determinate and indeterminate structures by examining the degrees of freedom of structural frames.
STEEL STRUCTURES IES MASTER GATE STUDY MATERIAL : CLICK HERE
The number of degrees of freedom of a structure denotes the independent movements of the structural members at the joints, including the supports. Hence, it is an indication of the size of the structural problem. The degrees of freedom of a structure are counted in relation to a reference coordinate system. External loads are applied to a structure causing movements at various locations. For frames, these locations are usually defined at the joints for calculation purposes. Thus, the maximum number of independent displacements, including both rotational and translational movements at the joints, is equal to the number of degrees of freedom of the structure. To identify the number of degrees of freedom of a structure, each independent displacement is assigned a number, called the freedom code, in ascending order in the global coordinate system of the structure
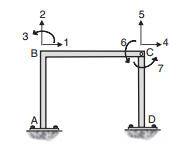
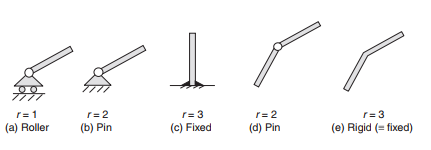
Plastic Design Concept
Plastic design makes use of the reserve strength beyond the elastic state of the structure. The structure’s reserve strength, which allows structural members to be loaded without failure when their maximum bending capacity is reached, is utilized through the elastic–plastic state when the loading is increasing. As a result, a more economical design due to material saving can be achieved when using the plastic design method. Plastic design can be viewed as a means whereby the ability of moment redistribution of steel structures is utilized when the structures are loaded beyond their elastic state. It may be noted that in adopting a bilinear moment–curvature relationship for steel, the beneficial effect of strain hardening of the material is ignored. Thus, as far as plastic analysis is concerned, the theoretical plastic collapse load is always less than the true load and the resulting design is always slightly conservative.
STEEL STRUCTURES ACE GATE STUDY MATERIAL : CLICK HERE
Comparison of Linear Elastic and Plastic Designs
For elastic design, each of the members in the structure must have a design bending moment capacity (ΦMs) greater than the design moment (M*) obtained from an elastic analysis. The bending moment capacity, calculated by including the appropriate capacity factor f and other design considerations, is often used to represent the plastic moment Mp in plastic analysis. Under the design loading, if one of the members meets the design requirement such that ΦMs = M*, the first plastic hinge occurs exactly at the design load level along the elastic design curve. In most cases, the choice of the section for elastic design leads to ΦMs > M* so that the first plastic hinge of the structure always occurs at a load level above the design loading. In contrast, plastic design requires that the last plastic hinge occurs at or above the design load level. It is clear that if both elastic and plastic designs satisfy the same design loading, the plastic design method requires a lighter structure with smaller member size by utilizing the reserve strength of the structure. It is noted that for a structure with a high degree of statical indeterminacy, the reserve strength is large. Therefore, the benefit of using plastic design is greater for structures with high degrees of statical indeterminacy. However, for determinate structures that require only one plastic hinge to induce a collapse, there is no difference between elastic and plastic design methods.
STEEL STRUCTURES ACE GATE NOTES : CLICK HERE
Limit States Design
Limit states design (LSD), also termed load and resistance factor design (LRFD) in the United States, is based on realistic loading conditions and material properties as opposed to allowable stress design (ASD), which is mainly based on prescribed loading and stress limits. Although the linear elastic design method can be applied to both LSD and ASD, only the latter is truly elastic. While linear elastic analysis is performed using the linear load–displacement relationship, elastic bending theory is applied to ASD for stress calculation, whereas for LSD, plastic bending theory is used for moment capacity calculation of the section. For steel structures, two major limit states need to be considered for general design: the ultimate limit state and the serviceability limit state. There are other limit states that may need special treatment and are usually classified under “accidental loadings” in design codes. In the present context, only ultimate and serviceability limit states are dealt with.
DESIGN AND PLASTIC ANALYSIS OF STEEL STRUCTURES TEXTBOOK BY CIVILENGGFORALL PDF
DOWNLOAD LINK : CLICK HERE
PASSWORD : CivilEnggForAll
OTHER USEFUL BOOKS
- RAJASTHAN STAFF SELECTION BOARD (RSSB) JUNIOR ENGINEER DIPLOMA CIVIL ENGINEERING EXAM 2022 – HINDI & ENGLISH MEDIUM SOLVED PAPER – FREE DOWNLOAD PDF (CivilEnggForAll.com)
- ISRO TECHNICAL ASSISTANT EXAM 2022 – CIVIL ENGINEERING – HINDI & ENGLISH MEDIUM – SOLVED PAPER – FREE DOWNLOAD PDF (CivilEnggForAll.com)
- MADHYA PRADESH PUBLIC SERVICE (MPPSC) COMMISSION – ASSISTANT ENGINEER EXAM – MPPSC AE 2021 CIVIL ENGINEERING – SOLVED PAPER WITH EXPLANATIONS – PDF FREE DOWNLOAD
- BIHAR PUBLIC SERVICE COMMISSION (BPSC) ASSISTANT ENGINEER EXAM – 2022 – CIVIL ENGINEERING – SOLVED PAPER – FREE DOWNLOAD PDF (CivilEnggForAll.com)
- ODISHA PUBLIC SERVICE COMMISSION – OPSC AEE PANCHAYATI RAJ EXAM 2021 – SOLVED PAPER WITH EXPLANATION – FREE DOWNLOAD PDF